
Manufacturing of various chemicals like esters, ethers, cumene, petroleum processing unit, etc. The optimization and sensitivity analysis was carried out using Aspen Plus process simulation software.Ĭhemical engineering deals with the conversion of raw material into products via a chemical unit process or unit operations. The result obtained was observed with change in various variables including the reflux ratio (RR), distillate-to-feed (D/F) ratio, and bottom-to-feed (B/F) ratio with respect to product composition. A strong acidic ion exchange catalyst, Amberlyst-15, was used to enhance the rate of heterogeneous esterification reaction. The synthesis of methyl acetate was carried out in a packed RDC by catalytic esterification using acetic acid and methanol as reactants in a pilot-scale experimental setup. The results are compared for both experimental and simulation studies. Methyl acetate production via reactive distillation is chosen as a case study. In this chapter, modeling, simulation, and optimization of reactive distillation are presented.
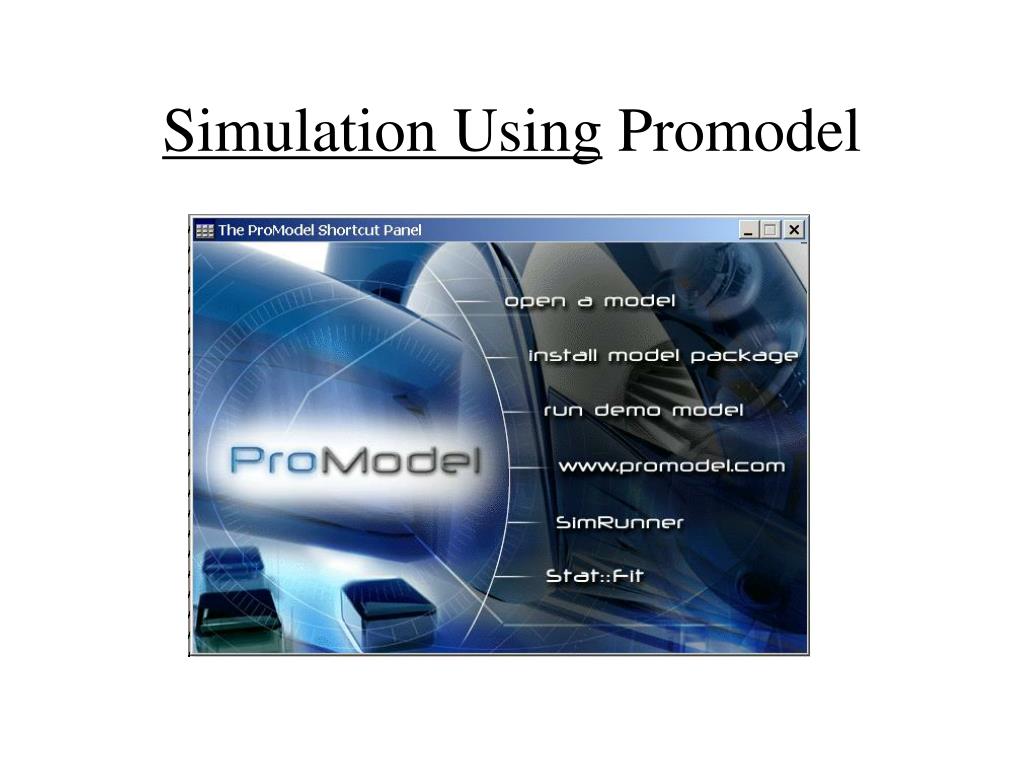
This makes it a highly complex process because many parameters involved in both reaction and separation are interactive in nature. Reactive distillation is a new technique of combination of both reaction and separation in a single unit beneficial for equilibrium-limited reactions and also cost-effective. Our recommendations are practical and based on sound engineering practices, while keeping operability and cost-effectiveness in mind.Chemical process industries deal with production which further utilizes reaction followed by separation of the reaction mixtures. We are particularly proud that so many of our clients return to us for process simulation services and that they continue to rely on us for integrity, insight and value. ioMosaic can conduct process simulation using commercially available software packages, such as ASPEN HYSYS or Invensys PRO/II, depending on client or project requirements.
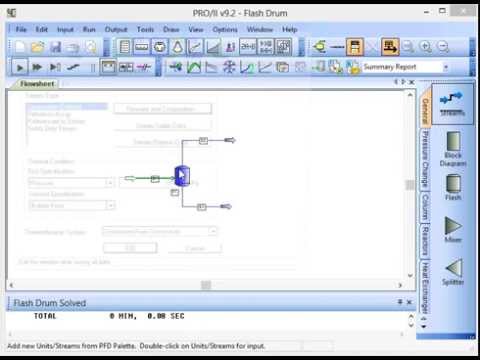
We have a wide range of process simulation project experience, ranging from refineries, chemical and petrochemical plants, pharmaceuticals and liquefied natural gas facilities.

This activity can be conducted independently, or integrated as part of a larger study, such as a flare and relief systems study. IoMosaic experts have extensive experience in developing process simulations, and heat and material balances. An accurate process simulation enables organizations to better and more accurately evaluate hazards in a facility. As well as being a code requirement, process simulations are integral to a comprehensive Process Hazard Analysis (PHA).Īn accurate heat and material balance is a key piece for Process Safety Information (PSI) for any facility. OSHA process safety management regulations require heat and material balances to be provided for processes built after May 1992.
